Mr. Mindl, PhD in Chemistry and 18 years of experience at Procter & Gamble’s production and quality management, joins KOH-I-NOOR to reinforce the services provided to our customers
published on Dec 23, 2023
share:
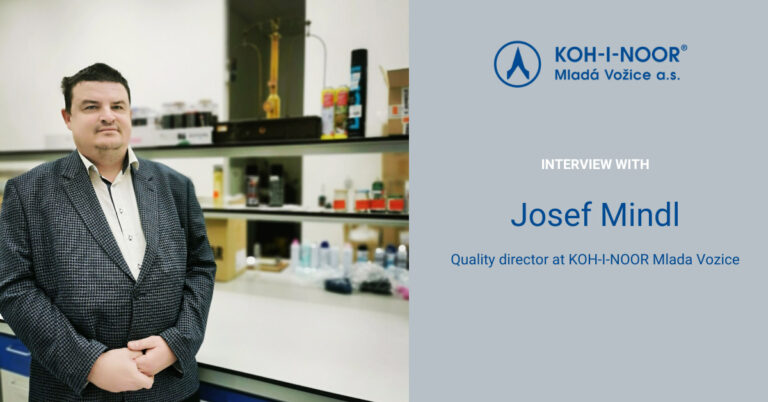
Procter & Gamble is undoubtedly an interesting work experience. What roles did you go through there, and can anything be transferred to our company?
Working at Procter & Gamble was challenging but also highly inspiring, providing me with substantial knowledge and practical skills.
From day one, I was responsible for the results of a production line (safety, quality, reliability). Within six months, I took on the responsibility of leading operators on that production line.
I learned that having technical knowledge alone is not enough; it’s essential to develop interpersonal skills. I used the English language on a daily basis, which was not common in the 1990s, as the company is multinational, enabling collaboration with colleagues worldwide. I was fortunate to build a capable and dynamic team, resulting in consistently good outcomes. For almost every manager at this company, a change in position occurred approximately every three years. Over the years, I progressed through roles in production management, quality, and research and development. I worked in three of the company’s production plants in Europe. The company’s mentality of continuous improvement in production processes and eliminating losses became my lifelong work philosophy.
I spent a total of 18.5 years of my life in this company and would definitely recommend it to any technical university graduate as their first employment. I realized the strong value of a corporate culture based on teamwork and respect for others’ opinions throughout the entire company. Machines and production halls can be bought, but the results come from specific people, who represent the company’s greatest wealth. I believe all these principles can be applied in any company.
It’s not about the starting point but how you define your goals and gradually work towards them.
Mr. Mindl, you have a doctorate in chemistry from university. What was the focus of your doctoral studies?
I graduated from the Faculty of Environmental Technology at the University of Chemistry and Technology in Prague.
Originally, I intended to work as a chemist specializing in water treatment and corrosion risk elimination for the newly constructed Temelín nuclear power plant after completing my studies. However, my path took a different turn as I enjoyed my studies and found them manageable. I decided to pursue a three-year postgraduate study in addition to my initial degree.
My doctoral thesis focused on the relationship between the structure of chemical substances and the inhibition of corrosion processes. At that time, I extensively utilized various electrochemical experimental methods for my work, combining them with theoretical calculations from the field of quantum chemistry.
How did you get into the field of quality, and why quality specifically?
I always understood that producing a product is not enough; the customer who pays for it must be satisfied. The customer is not interested in whether the manufacturer produces 100 or 1000 units per hour but rather if the product works and meets all requirements.
I have been guided by the principle of “better less but thorough” since my youth. When I started my first job in the industry as a drying tower technologist in the production of laundry detergent, I was immediately confronted not only with safety results but also with the quality of the product. Quantity came later.
What impressed you the most about KOH-I-NOOR’s corporate culture and values?
I must say that the exceptionally clean environment, order in production, and ample lighting in the manufacturing areas made the greatest impression on me. I believe these elements form the foundation for excellent results in safety and quality. I particularly appreciate teamwork, where everyone can express their views without fear.
What’s important to me is that I haven’t sensed any mutual rivalry here; rather, it’s about complementing each other, following the philosophy of “the more heads, the more ideas.”
How would you describe your working style?
I would describe my working style as “calm strength.”
Personally, I dislike stress, but I can cope with it when necessary. I understand that when an urgent problem arises, it needs to be addressed immediately. On the other hand, I prefer systematic work, providing the opportunity to continuously improve things step by step.
This aligns with the philosophy of my work, which is based on data and numbers. I cannot imagine doing a job without knowing where I stand.
How do you strive to maintain your professional skills and learn new things in the field?
In terms of technical knowledge, I heavily rely on the internet. Today, you can watch specialized lectures on platforms like YouTube from institutions such as Harvard, MIT, or Oxford on almost any topic. I subscribe to a magazine in the field of chemical technology that includes contacts for various manufacturing companies and their presentations. This keeps me informed about industry developments.
Since finishing school 25 years ago, science and technology have progressed incredibly. I also value soft skills, which may be even more critical for managerial positions. I highly recommend Stephen Covey’s book, “The 7 Habits of Highly Effective People,” which has been a source of inspiration for me for 20 years.
You’ve held positions in quality, production, and technology in various companies. What has each phase of your career provided you?
When I started my first position, I had a lot of knowledge but also a naive belief that I could solve everything on my own. I thought that working hard would automatically yield results. Over time, I realized that I needed to work smartly and utilize not only my own knowledge but also that of others. Good results are a result of everyone’s efforts, and everyone benefits from them.
I’ve held several leadership positions, but the greatest satisfaction came from successful projects or the implementation of new systems where everything worked, and I could move on to the next challenge.
Throughout my career, I had the opportunity to work in several countries, both highly developed and developing. Experiencing different mentalities and cultures gave me a broader perspective on my work and on the Czech Republic.
I believe we have great potential here. Originally from South Bohemia, I was glad to return to this region almost 30 years later. I think the time has come for me to give something back to this region.